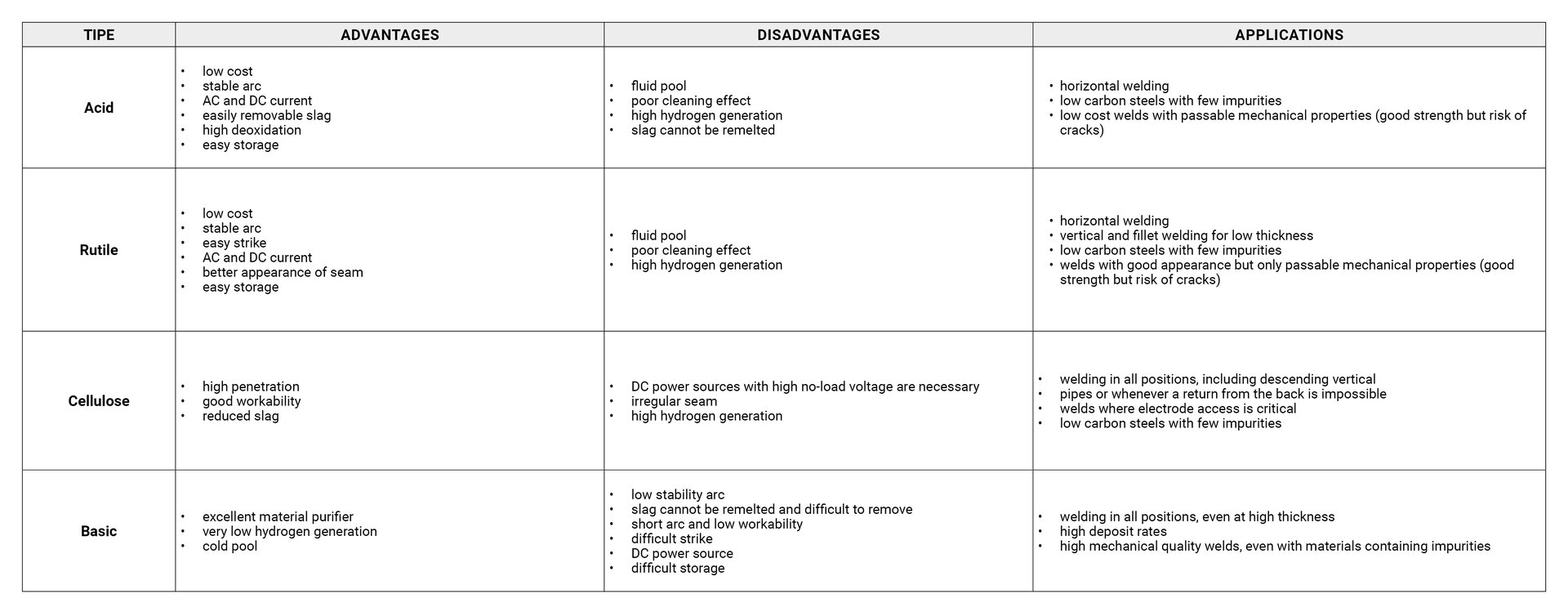
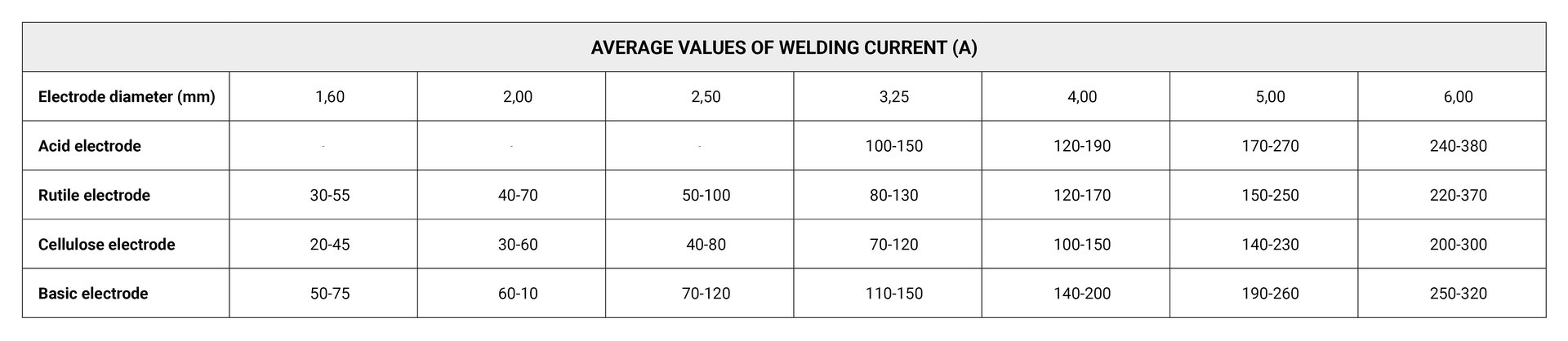
Products
PPE & Safety
Accessories and Consumables
Products
Industries
Corporate
Knowledge Center
1. FEATURES
The coated electrode consists of a core and a coating: the core consists of a metal conductor rod whose sole purpose is to supply welding material to the piece.
The material used depends on the base material: for carbon steels, for which electrode welding is most widespread, the core is in mild steel. During welding the core melts slightly before the coating does. The coating is the most important part of the electrode and has many functions. It primarily serves to protect the weld from air contamination, and it achieves this in different ways.
By volatilizing, and then modifying the atmosphere surrounding the weld pool; by delay melting and consequently by protecting the core with the naturally formed crater; and by liquefying and floating on top of the pool. It also contains material capable of purifying the base material and elements that could contribute to the creation of alloys in the melt. The choice of coating is therefore very important and depends on the characteristics to be given to the weld. The coating can also contain weld material as a powder, to increase the quantity of deposited material and hence the welding rate. In this case we refer to high performance electrodes.
2. ELECTRODE CATEGORIES
Various types of coated electrodes are available on the market, and their chemical composition has a strong influence on electric arc stability, penetration depth, material deposit, pool purity i.e. on their fields of application.
According to the coating type, the main types of electrodes are:
The coatings of these electrodes consist of iron oxides, iron alloys of manganese and silicon. They ensure good arc stability making them suitable for both alternating current (AC) and direct current (DC). They have a very fluid weld pool which makes welding in position impossible; moreover, they do not have a great ability to clean the base material and this could cause cracks. They will not withstand high drying temperatures, with the consequent risk of residual humidity and therefore hydrogen inclusions in the weld.
The coating of this electrode consists essentially of a mineral called rutile. This consists of 95% titanium dioxide, a very stable compound that ensures optimum arc stability and high weld pool fluidity, which has a noticeable effect on the appearance of the weld. The function of the rutile coating is, however, to ensure a soft melt that is easy to realise, and facilitates the formation of an abundant, viscous slag that gives good flowability into the weld, especially in a horizontal position. In this case the seam has a pleasing, regular appearance. Unfortunately, like the above, these coatings are not very effective cleaners either, so they are recommended when the base material does not contain many impurities; moreover, they cannot be dried perfectly so a large quantity of hydrogen is generated in the weld.
In some applications rutile is combined with another component that is typical of other coatings, such as cellulose (rutilcellulose electrodes) or fluorite (rutilbasic electrodes). Their usual purpose is to obtain an electrode with a stable arc that gives a higher performance weld.
Arc stability is a property that enables this electrode to be used with both alternating current (AC) and direct current (DC) in straight polarity. It is mostly used on low thicknesses.
The coating of these electrodes consists mainly of cellulose integrated with iron alloys (magnesium and silicon). The coating gasifies almost completely, thus allowing welding in a descending vertical position, which cannot be achieved with other types of electrode; the high gasification level of the cellulose reduces the quantity of slag present in the weld. The generation of a large quantity of hydrogen (derived from the particular chemical composition of the coating) ensures a "hot" weld pool, with the melt of a considerable quantity of base material; it is thus possible to obtain high penetration welds with little slag in the pool.
The mechanical properties of the weld are optimal; the appearance is rather poor since the almost complete absence of liquid protection given by the coating does not allow the pool to be shaped during solidification.
Given the poor arc stability, the welding current is usually direct (DC) with reverse polarity.
The coating of basic electrodes consists of iron oxides, iron alloys and primarily calcium and magnesium carbonates which, with the addition of calcium fluoride, obtain fluorite which is a mineral used to facilitate melting. They have a high base material purification capacity, so that high quality welds are obtained with considerable mechanical strength. These electrodes also withstand high drying temperatures so that they do not contaminate the pool with hydrogen. Fluorite makes the arc very unstable: the pool is less fluid, there are frequent short circuits due to the transfer of large drops of weld material; the arc should be kept very short due to the low volatility of the coating; all these properties need the presence of an experienced welder. The welds have a hard slag which is difficult to remove, but must be completely removed for repeated passes. These electrodes are suitable for horizontal, vertical and overhead welding.
As regards the current to be employed, the use of direct current (DC) power sources with straight polarity is recommended. Basic electrodes are distinguished by the very high quantity of material deposited and are well adapted to welding high thickness joints. They are very hygroscopic and should be kept in a dry place in a hermetically closed container; if this is impossible, we recommend drying the electrode again before using it.
3. PROPERTIES OF THE VARIOUS TYPES OF ELECTRODES
4. CHOICE OF CURRENT FOR THE VARIOUS TYPES OF ELECTRODE
5. CLASSIFICATION OF THE ELECTRODES
According to the standard EN 499, coated electrodes are classified into groups depending on the type of coating and their most important properties.
a) According to current standards, each electrode can be completely defined by an identification given on the package cover, as in the example below:
E44T3C19R09KV20
The meaning of which is given here below:
* E = electrode
* 44 = tensile strength, which can be:
00 = no guaranteed value;
44 = minimum guaranteed value 44 Joule
* T = Type of application which can be:
S = for thin sheets (below 4 mm.);
L = for medium and thick sheets;
T = for piping.
* 3 = quality class, which can be from 1 to 4, increasing as particular mechanical tests are passed.
* C = Type of coating, which can be:
R = rutile RC = rutile cellulose
B = basic RB = rutile-basic
C = cellulose V = special (to be specified on the package)
* 1 = welding positions, which can be:
1 = all
2 = all, excluding descending vertical
3 = only horizontal and frontal-horizontal (normal angle)
4 = only horizontal and positioned angle.
* 9 = current to be used, which can be:
* R09 = minimum guaranteed efficiency, expressed in tenths;
* KV20 = extra symbol for low temperature impact resistance properties; in the example the electrode has an impact resistance value down to -20 °C.
b) Given the increasing use of the AWS (AMERICAN WELDING SOCIETY) and ASTM (AMERICAN SOCIETY FOR TESTING AND MATERIALS) classification among Italian users, each electrode is described by the manufacturer's logo as well as by a symbol as in the following example:
E6011
The meaning of which is reported here below:
E = electrode
60 = minimum tensile strength, expressed in pounds per square inch
1 = welding positions which can be:
1 = all
2 = horizontal and positioned angle
1 = welding current, which can be:
0 = direct with electrode negative polarity, for cellulose electrodes;
1 = alternating and direct (positive pole)
2 = alternating and direct (negative pole)
3 = alternating and direct for rutile electrodes
4 = alternating and direct for high performance rutile electrodes
5 = direct with electrode negative polarity for basic electrodes
6 = alternating and direct for basic electrodes
7 = alternating and direct (any pol.or neg.pole only) for high performance iron oxide
8 = alternating and direct (positive pole) for high performance basic electrodes.